Background to Melbourne brickcleaning
Over the last 30-40 years the cleanliness of the general finished quality of the brick work in Melbourne has deteriorated to being arguably the worst in Australia and probably the worst in the world. Builders and supervisors have accepted this poor workmanship and have hidden or stopped monitoring the consequential financial costs to repair the damage caused by Hydrochloric Acid from cleaning these jobs because they had no alternative. Even worse is the fact that they have a mechanism in their contracts to recover costs from the brickies and cleaners if it goes wrong. Therefore they have eliminated any responsibility to try to make sure that they are laid clean and in a state that they can be cleaned without damage from acid treatments. Even OH&S managers have had to accept the risks of Hydrochloric acid being on site. Barracuda 10K offers a solution to this. See below.
In Melbourne very few builders or supervisors have a bricklaying background nor have they the time to understand how to lay bricks cleanly and mix mortar correctly, so the bricklaying quality can be very low (see below for typical examples). Forty years or more of a continued shortage of bricklayers has exacerbated the problem. Builders continually lowered their standards and took on anyone to get their work done on time. This led to an acceptance of the poor quality of workmanship shown below (pictures) while the use of pressure washing with acid grew simultaneously as an alternative fast and cheap cleaning method. This helped cover up the deterioration of the poor finishing quality. Collateral damage by acid was ignored, not costed, and became acceptable as there was no perceived alternative and the art of laying clean has become ignored and even worse forgotten.
As Melbourne bricklayers became divorced from any cleaning responsibility, the knowledge of how to lay cleanly and what makes a job hard to clean has been lost. This has allowed bricklayers here many bad practices e.g. like not buttering up enough, jointing and brushing green mortar, eliminating the second cut so the bricks end up with heavy deposits of thick sandy mortar. Many bricklayers now think that the brick cleaner should clean everything. They don't understand nor do they care about the brick cleaner's problems, as they have no comprehension about how difficult it is to clean thick aged hardened and plasticized sandy mortar left by dirty bricklaying. They expect that it will all be cleaned regardless of how dirty they leave the finished brick work. When I have discussed this with them, they resent and actively resist any requests for changes. The usual answer is they don't get paid enough to lay cleanly or make any changes. The jobs these types of bricklayers leave are almost impossible to clean without damage and they certainly cannot be cleaned without damage within contract pricing limits demanded by builders. It is also interesting to note that clean bricklaying can be faster than dirty bricklaying when done properly.
Another compounding factor is that bricklayers often have to repair holes and blowouts after the brickclean. When they see the damage done by the acid cleaners, they add more cement and make stronger mortars, on subsequent jobs, in an attempt to prevent this damage from occurring again. Unfortunately this has only led to an increase in the damage they get, as the brick cleaners have to use much more or stronger acid, higher pressures and more washes to clean this excessively hardened mortar, especially if it was left dirty. Some also try to use plasticiser and lime replacements to strengthen it even more but this too has only exacerbated the cleaning damage and has added extra levels of complication.
Other influencing factors, in the deterioration of mortar beds and increase in brick stains in Melbourne, was the introduction of 20 Kg bag of Cement that stated that a 6:1:1 mix should be used. This meant that the laborers began dumping a whole 20 kg bag in the mixer before adding sand and lime. Unfortunately mixers only allow about an additional 18 - 24 shovels of sand before they overflow and these never add up to to 120KG, so the standard mix had even more cement added and became even harder. In fact there are about 7.5 post hole shovels in in bag of cement, so a 6:1:1 mix should have approximately 30 shovels of sand. This is impossible as mixers will not accept this much so the standard 6:1:1 mix is more like a 3 or 3.5:1:1 mix. So most Melbourne mortar is far too hard and almost impossible to clean with acid without damaging the mortar beds or preventing acid burn. Also the practice of back-charging for soft mixes and making bricklayers responsible for the repair, at their cost, has led many bricklayers to add a precautionary extra shovel or two of cement in each mix, in an attempt to protect their mortar by hardening it even more. These series of seemingly logical steps has helped created the dirtiest bricklaying with the hardest and stickiest mortar in Australia and perhaps the world which is the route cause of most of the damaged mortar in Melbourne.
For the above reasons, over time in Melbourne the AS3700 standard M3 mortar mix (M3 =6 sand : 1 Lime : 1 Cement) & M2 mortar mix (M2 =9 sand : 2 Lime : 1 Cement) for under roofing and above damp course use has changed and the new standard mix in Melbourne seems to have become a very strong M4 or mix which is a chemical resistant mix good for a salt coast or chemical environment. Unfortunately these bricks are now being laid with very little cutting or dry brushing and no sponging. When acid is used to clean these excessively dirty, hardened, plasticized thick deposits, it is inevitable that it will attack the same amount of mortar (depth) in the beds making it almost impossible for brick cleaners to prevent acid damage. This why there are so many houses with sandy, rough, friable, pitted, and blown out mortar beds in Melbourne (See last three images below). Even the by-products of acid left in the mortar beds are acidic and become reactive when it moistens in the rain so the destruction will slowly continue over time.
Builders too, have mandated harder mixes with the same false reasoning, hoping that this will help prevent the damage they are experiencing from acid washing. Very few have demanded clean laying which is the most important factor to prevent damage while cleaning, especially as the mortar is now becoming harder and being cleaned later. Occasionally a builder has made the bricklayers responsible to clean their work and it doesn't take long for the quality of the finish to improve when this happens but these campaigns seem short lived. The basic fact is that Builders are responsible for all the products on their houses as they have the licence to build but they dont understand mortar. They insist on the lowest cost cleaning option but dont allow for the fact that every bricky makes a different mix and leaves a different finish which make the clean more difficult. Builders need to control the quality of the bricklaying if they want to fix costs. Surely if they want a quality product they need to control the input quality. The sad fact is none many do this properly in Melbourne even if they think they do.
Brick manufacturers too, have expanded the range and types of bricks sold in the last 40 years and this has increased the complexity of cleaning and laying, so the heydays of easy washing of solid reds, browns and yellow bricks has long gone. We now have solids, dry pressed and concrete bricks and numerous slurry coating colours including metallic and glossy coatings. Best practice manufacturing changes to the kiln designs, fuels and temperatures, changes in cement chemistry (much higher MPA ratings), the addition of superplasticizers (admixtures) from the concrete industry and imported bricks made with different technology from totally different clays make it easy to understand why cleaning problems have increased.
Many Melbourne brick cleaners (acid washers) have done a tremendous job as they have learned how to use acid, turbo heads and fan nozzles to clean, shape and restructure hard mortar beds that were left uncut and unbrushed with excessively thick splatter and smeared mortar on the brick face (up to 8-16 mm thick). We often see jobs with aged and extremely hard mortar that were rolled with a piece of plastic pipe found onsite and not even cut or dry brushed. It is impossible to clean these jobs and leave a sharp crisp polished mortar bed finish. When plasticisers and white cements are used in the mix the mortar becomes even harder and stickier. These j0bs become impossible to clean without damage, especially in the time frame that builders costings allow. Plasticizers and the use of the new high MPA cements has increased the hardness and thus the degree of difficulty to clean and this has increased the time required to clean these jobs by 3 to 5 fold or more. Most builders will not pay for this extra time until they learn from bitter experience the costs involved to fix the damage done by"the Estate Acid Washing Turbo Warriors" trying to clean these hard dirtily laid jobs with mortars laden with admixtures cheaply with acid and turbos is nothing compared to the cost of proper rectification.
Some acid washers have become very skilled at preventing damage but they are in short supply and are much more expensive. I call them the "Fan, Scratch and Scrape Brigade". They usually have their loyal customers who know from experience how much an acid washer can affect the cost, look and quality of a job more than any other trade. Volume builders who don't want to pay this type of work have held down the cost of acid washing by pricing it on a $/thousand bricks and their Construction and Site Manager control systems do not allow them any contingency for brick type, mortar mixes and hardness, poor laying or dirty workmanship. In response many of the acid washers servicing these builders have started using 2:1 or 1:1 acid: water mixes to get the clean done in time. This has led to what I call the "The Art of Acceptable Collateral Damage" as the standards accepted by builders have lowered over time. This has had a consequential effect and has led to the destruction of mortar beds, soft faced bricks, roofs and fascias as well as salt staining and Iron staining. The volume builder acid washers have had to become very fast and extremely skilled at applying strong acid to clean this volume work and I call them the "Acid Washing Estate Turbo Warriors". Supervisors too, have accepted this "turbo" workmanship as standard practice although it is frowned upon, but not stopped. Unfortunately when there are problems they can blame and back charge the acid washer as they were the last trade to touch the bricks and the contracts are written so they can do this. This is unfair and generally incorrect as its the quality of the brick laying and the builders lack of knowledge and tolerance of this poor workmanship that has allowed the situation to develop .
The one irrefutable fact is that every Melbourne Brick layer has his own mix, so each job is different and there are no common standards. This is a classic example of an industry in disarray so it is totally understandable that the acid cleaners, brick layers and builders struggle with all these complexities I believe, from my experiences, that this summarizes many of the reasons why so many houses have damaged mortar and bricks in Melbourne and outlines the reasons why 80-90% of the new builds now no longer meet code.
barracuda 10k can help with these problems:
Photo Examples Below:
The pictures below show some poor bricklaying as well as the results of cleaning poorly laid jobs. The potential of Barracuda 10K is shown as well.
Some of the brick work shown below has had thick mortar deposits up to 10 mm and more smeared on the brick face and the edges. They were not cut or dry brushed (or sponged) clean when laid and scaffold splatter was left on the bricks to harden as well. To clean these properly, additional hand scraping, turbo cleaning, even sandpapering or grinding will be required to prepare these houses for a decent brick clean and this takes a lot of time and will cost a lot more. Surely it is best to clean before the mortar is hard and has set.
.


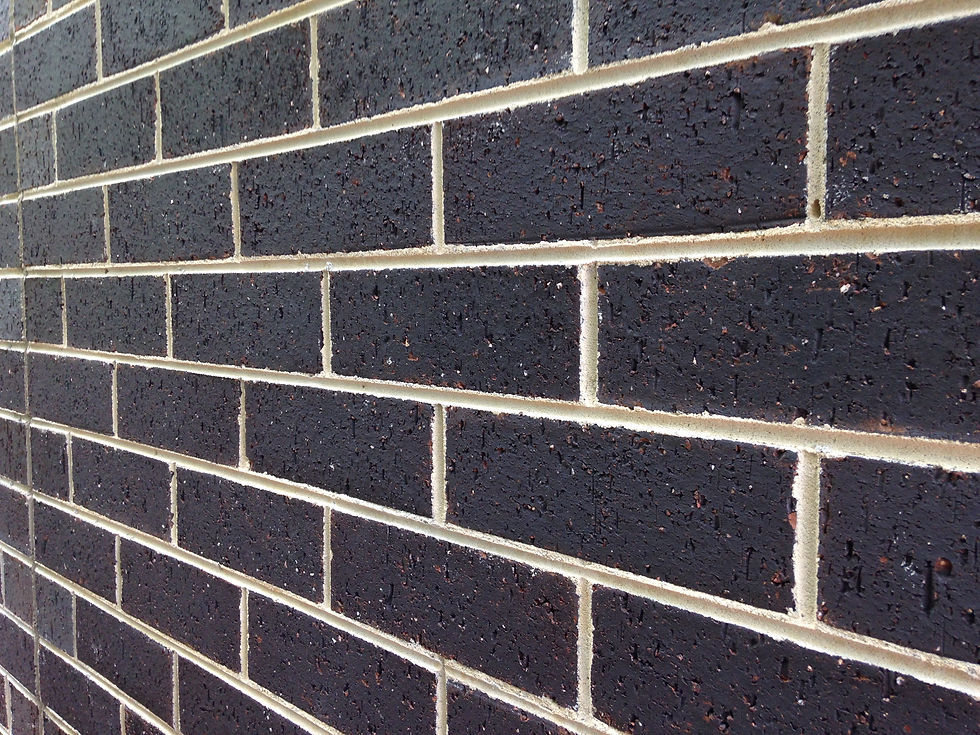
good result with poor bricklaying but good mortar






Brick layers with 20 years experience


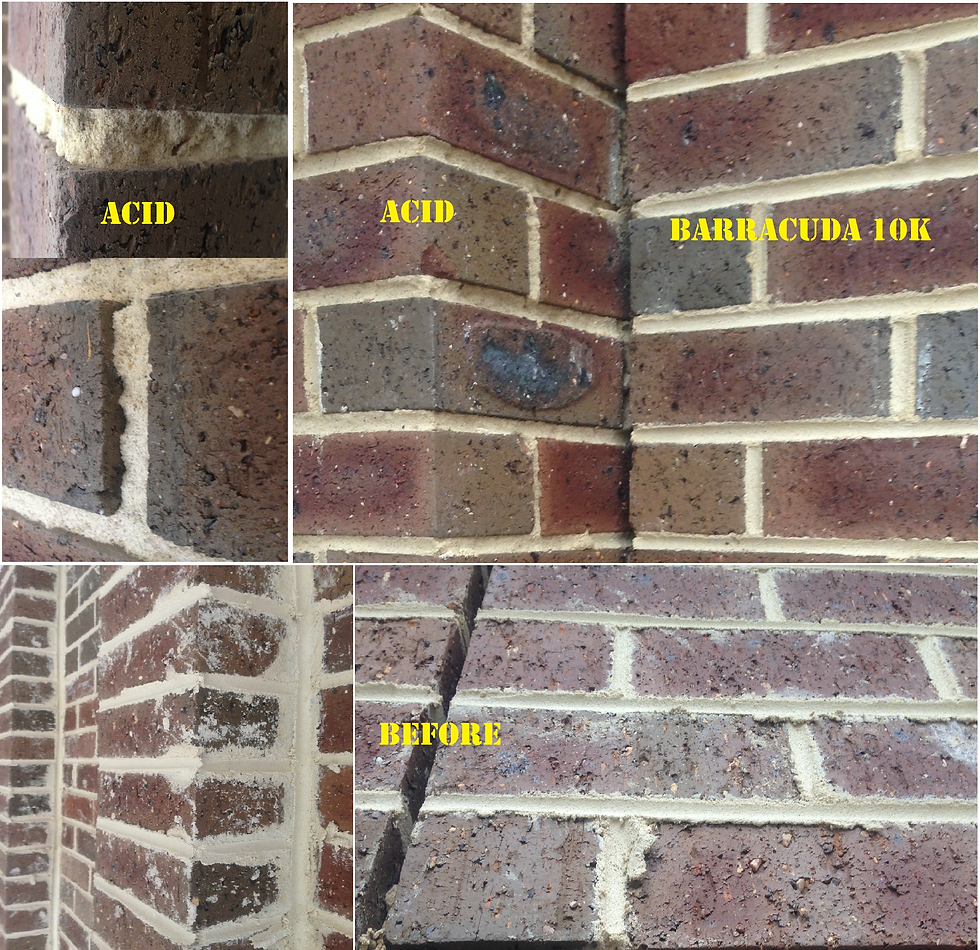


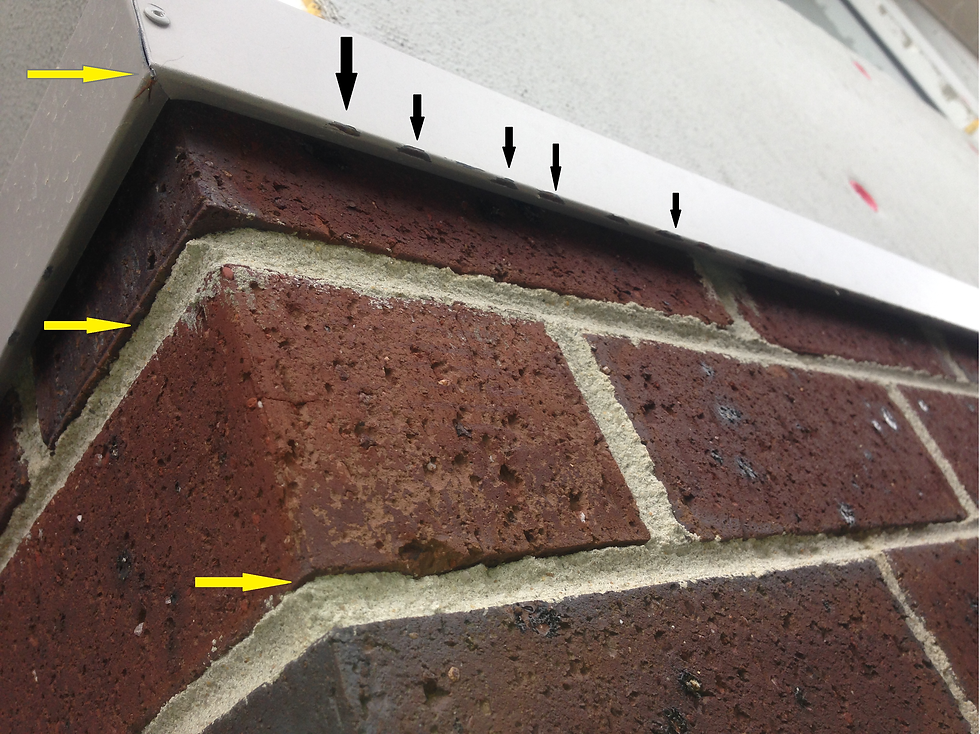



Before washing